concrete batching plant Centrales A Beton
Concrete batching plants are essential facilities in the construction industry, designed to produce concrete in a consistent, efficient, and timely manner. These plants combine various ingredients such as water, cement, aggregates, and additives to create high-quality concrete. This article provides an introduction to concrete batching plants, discussing their capacities, types, mixer hosts, and other critical components.
Capacities of Concrete Batching Plants
Concrete batching plants come in various capacities, catering to different project sizes and requirements:
- Small Capacity (15-50 cubic meters per hour): Ideal for small-scale projects like residential buildings, small roads, and repair works.
- Medium Capacity (50-150 cubic meters per hour): Suitable for medium-sized projects such as commercial buildings, medium-sized roads, and urban infrastructure projects.
- Large Capacity (150+ cubic meters per hour): Designed for large-scale projects including highways, bridges, high-rise buildings, and significant infrastructure developments.
Stationary vs. Mobile Batching Plants
Concrete batching plants can be classified into stationary and mobile types based on their mobility and installation:
1. Stationary Batching Plants
Stationary batching plants are installed at a fixed location and are ideal for projects with a long duration or where the concrete production facility needs to stay in place.
- Advantages:
- Higher production capacity.
- Better consistency and quality control.
- Suitable for large-scale projects.
- Disadvantages:
- Requires a significant setup time and cost.
- Less flexible in terms of location changes.
2. Mobile Batching Plants
Mobile batching plants are designed for flexibility and can be easily transported and installed at different sites.
- Advantages:
- Quick setup and dismantling.
- Can be moved to different project sites.
- Ideal for short-term projects and remote locations.
- Disadvantages:
- Generally lower production capacity compared to stationary plants.
- May have slightly lower precision in batching.
Mixer Hosts: Twin Shaft Mixer vs. Planetary Mixer
The mixer host is a critical component of a concrete batching plant, responsible for the actual mixing of the ingredients. Two common types of mixer hosts are twin shaft mixers and planetary mixers.
1. Twin Shaft Mixers
Twin shaft mixers are known for their high efficiency and ability to produce large volumes of concrete quickly.
- Advantages:
- High mixing efficiency.
- Suitable for producing a wide range of concrete types, including high-strength concrete.
- Uniform mixing and consistent quality.
- Disadvantages:
- Higher initial cost.
- Requires more maintenance compared to other types.
2. Planetary Mixers
Planetary mixers are designed for producing high-quality concrete with excellent homogeneity.
- Advantages:
- Excellent mixing performance and homogeneity.
- Ideal for producing precast concrete, high-performance concrete, and decorative concrete.
- Lower maintenance requirements.
- Disadvantages:
- Lower production capacity compared to twin shaft mixers.
- Slower mixing process.
Batching Machine Bins Quantity
The batching machine, or aggregate batching system, is responsible for accurately weighing and batching the various aggregates used in the concrete mix. The number of bins in a batching machine can vary, influencing the plant’s efficiency and flexibility.
- Two Bins: Suitable for simple concrete mixes with fewer aggregate types.
- Three Bins: Offers more flexibility and precision, ideal for standard concrete mixes.
- Four or More Bins: Provides the highest level of flexibility, allowing for complex mixes with multiple aggregate types.
Conclusion
Concrete batching plants are versatile and essential in the construction industry, catering to a wide range of project needs with their varying capacities, types, and configurations. Whether stationary or mobile, equipped with twin shaft or planetary mixers, and featuring different numbers of batching bins, these plants are designed to produce high-quality concrete efficiently. Understanding the specific requirements of your project will help in selecting the right batching plant, ensuring optimal performance and consistent concrete quality.
Introduction aux Centrales à Béton : Capacités, Types et Caractéristiques Clés
Les centrales à béton sont des installations essentielles dans l’industrie de la construction, conçues pour produire du béton de manière cohérente, efficace et rapide. Ces centrales combinent divers ingrédients tels que l’eau, le ciment, les granulats et les additifs pour créer du béton de haute qualité. Cet article fournit une introduction aux centrales à béton, discutant de leurs capacités, types, malaxeurs et autres composants essentiels.
Capacités des Centrales à Béton
Les centrales à béton existent en différentes capacités, répondant à divers besoins et tailles de projets :
- Petite Capacité (15-50 mètres cubes par heure) : Idéale pour des projets de petite envergure comme les bâtiments résidentiels, les petites routes et les travaux de réparation.
- Capacité Moyenne (50-150 mètres cubes par heure) : Convient aux projets de taille moyenne tels que les bâtiments commerciaux, les routes de taille moyenne et les projets d’infrastructure urbaine.
- Grande Capacité (150+ mètres cubes par heure) : Conçue pour des projets de grande envergure incluant les autoroutes, les ponts, les immeubles de grande hauteur et les développements d’infrastructure importants.
Centrales Stationnaires vs. Mobiles
Les centrales à béton peuvent être classées en types stationnaires et mobiles en fonction de leur mobilité et de leur installation :
1. Centrales Stationnaires
Les centrales stationnaires sont installées à un endroit fixe et sont idéales pour des projets de longue durée ou lorsque l’installation de production de béton doit rester en place.
- Avantages :
- Capacité de production plus élevée.
- Meilleure cohérence et contrôle de la qualité.
- Convient aux projets de grande envergure.
- Inconvénients :
- Nécessite un temps et un coût d’installation significatifs.
- Moins flexible en termes de changement de lieu.
2. Centrales Mobiles
Les centrales mobiles sont conçues pour la flexibilité et peuvent être facilement transportées et installées sur différents sites.
- Avantages :
- Installation et démontage rapides.
- Peut être déplacé sur différents sites de projet.
- Idéale pour les projets de courte durée et les emplacements éloignés.
- Inconvénients :
- Capacité de production généralement inférieure par rapport aux centrales stationnaires.
- Peut avoir une précision légèrement inférieure dans le dosage.
Malaxeurs : Malaxeur à Double Arbre vs. Malaxeur Planétaire
Le malaxeur est un composant critique d’une centrale à béton, responsable du mélange réel des ingrédients. Deux types courants de malaxeurs sont les malaxeurs à double arbre et les malaxeurs planétaires.
1. Malaxeurs à Double Arbre
Les malaxeurs à double arbre sont connus pour leur haute efficacité et leur capacité à produire rapidement de grands volumes de béton.
- Avantages :
- Haute efficacité de mélange.
- Convient pour produire une large gamme de types de béton, y compris le béton à haute résistance.
- Mélange uniforme et qualité constante.
- Inconvénients :
- Coût initial plus élevé.
- Nécessite plus d’entretien par rapport à d’autres types.
2. Malaxeurs Planétaires
Les malaxeurs planétaires sont conçus pour produire du béton de haute qualité avec une excellente homogénéité.
- Avantages :
- Excellente performance de mélange et homogénéité.
- Idéal pour produire du béton préfabriqué, du béton haute performance et du béton décoratif.
- Moins d’entretien requis.
- Inconvénients :
- Capacité de production inférieure par rapport aux malaxeurs à double arbre.
- Processus de mélange plus lent.
Quantité de Bacs de la Machine à Dosage
La machine à dosage, ou système de dosage des agrégats, est responsable de peser et de doser avec précision les différents agrégats utilisés dans le mélange de béton. Le nombre de bacs dans une machine à dosage peut varier, influençant l’efficacité et la flexibilité de la centrale.
- Deux Bacs : Convient pour des mélanges de béton simples avec moins de types d’agrégats.
- Trois Bacs : Offre plus de flexibilité et de précision, idéal pour des mélanges de béton standard.
- Quatre Bacs ou Plus : Fournit le plus haut niveau de flexibilité, permettant des mélanges complexes avec plusieurs types d’agrégats.
Conclusion
Les centrales à béton sont des dispositifs polyvalents et essentiels dans l’industrie de la construction, répondant à une large gamme de besoins de projets avec leurs différentes capacités, types et configurations. Qu’elles soient stationnaires ou mobiles, équipées de malaxeurs à double arbre ou planétaires, et disposant de différents nombres de bacs de dosage, ces centrales sont conçues pour produire du béton de haute qualité de manière efficace. Comprendre les exigences spécifiques de votre projet vous aidera à choisir la centrale appropriée, garantissant des performances optimales et une qualité constante du béton.
Mobile concrete batching plant MP18
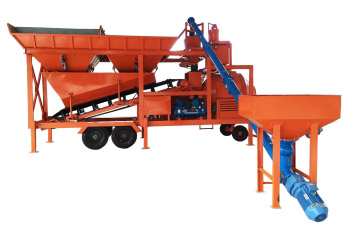
Mobile concrete batching plant MP25
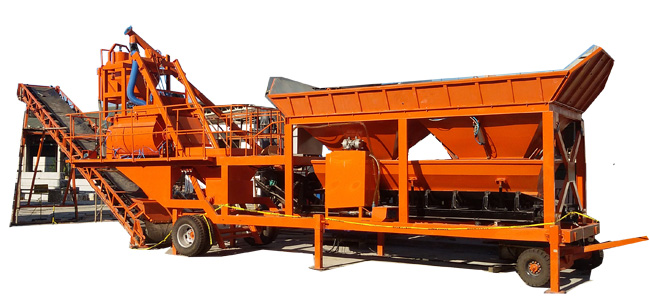
Mobile concrete batching plant MP35
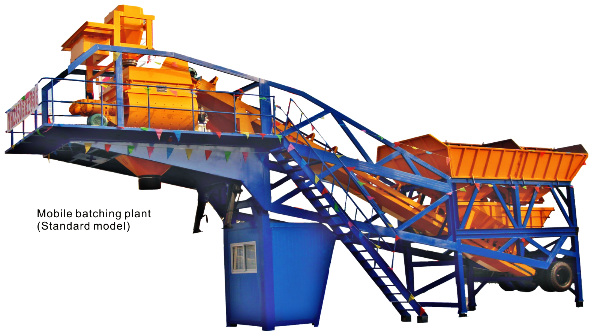
Mobile concrete batching plant MP60
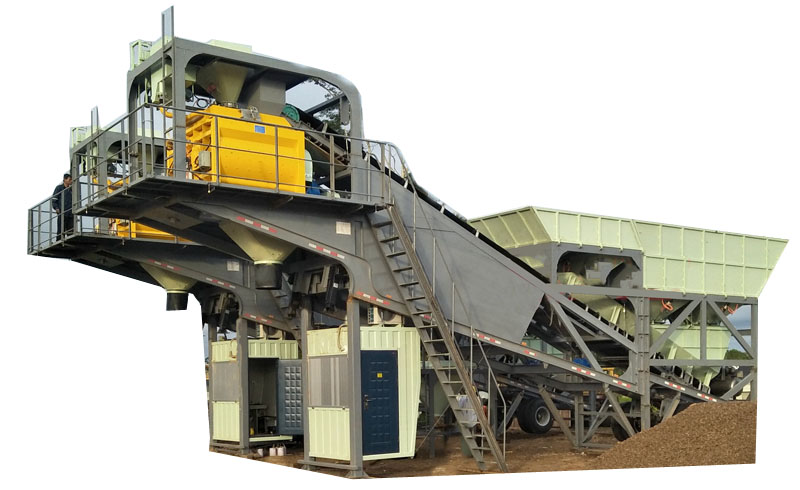
Stationary concrete batching plant CBP30
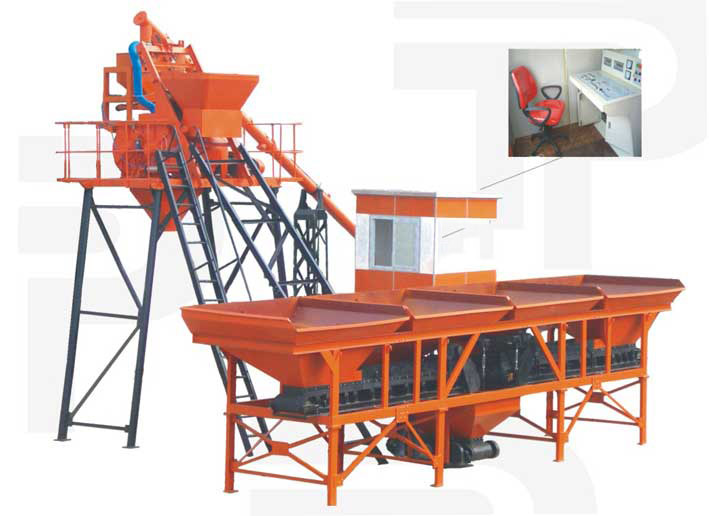
Stationary concrete batching plant CBP45
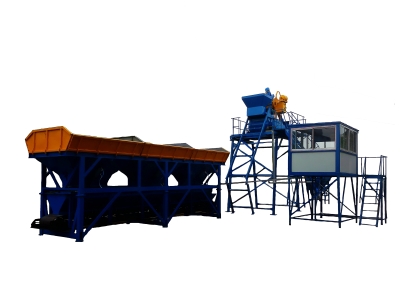
Stationary concrete batching plant CBP60
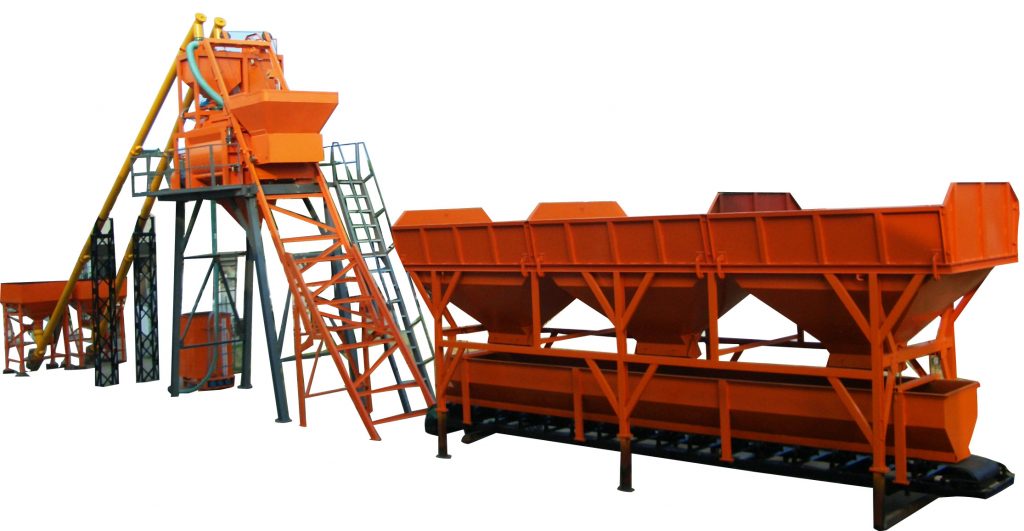
Stationary concrete batching plant CBP90
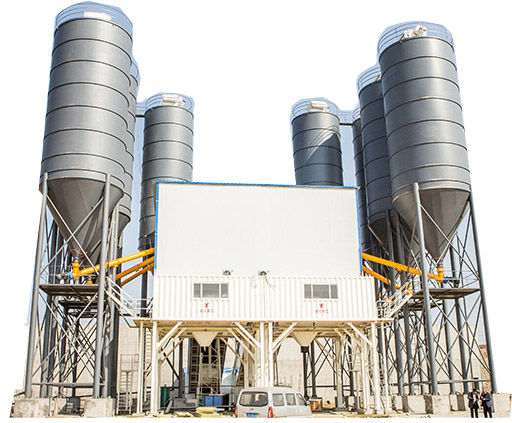
Stationary concrete batching plant CBP120
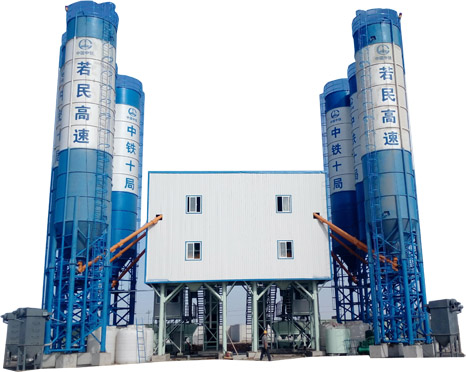